Efektywne zarządzanie produkcją wymaga nie tylko doskonałej organizacji pracy, ale również stałego monitorowania i analizy danych. Kluczowym narzędziem w tym procesie są wskaźniki produkcyjne (KPI), które pozwalają firmom przemysłowym podejmować trafne decyzje operacyjne i strategiczne. W artykule wyjaśniamy, dlaczego wskaźniki mają tak ogromne znaczenie, jakie są najważniejsze wskaźniki na produkcji, a przede wszystkim dlaczego OEE uznaje się za najistotniejszy wskaźnik efektywności produkcji.
Spis treści:
- Dlaczego wskaźniki są kluczowe w zarządzaniu produkcją?
- Które wskaźniki produkcyjne warto mierzyć?
- OEE – król wskaźników efektywności produkcji.
- Błędy przy interpretacji wskaźników produkcyjnych.
- Alternatywy i uzupełnienia dla OEE.
- Jak dobrać wskaźnik do typu produkcji?
- Wskaźniki a rozwój firmy – kiedy prostota, kiedy zaawansowanie?
- Jakie narzędzia wspierają monitorowanie wskaźników?
- Najważniejszy wskaźnik to… ten, który prowadzi do działania.
Dlaczego wskaźniki są kluczowe w zarządzaniu produkcją?
W środowisku produkcyjnym wszystko, co da się zmierzyć, można poprawić. Wskaźniki KPI umożliwiają firmom:
- identyfikowanie wąskich gardeł,
- redukcję strat i marnotrawstwa,
- optymalizację zasobów,
- podnoszenie jakości produktów,
- planowanie rozwoju i inwestycji na podstawie danych,
- motywowanie zespołu do osiągania celów.
Bez precyzyjnych wskaźników trudno efektywnie kierować produkcją, ponieważ brak danych uniemożliwia ocenę sytuacji, reagowanie na zmiany i dążenie do doskonałości operacyjnej.
Które wskaźniki produkcyjne warto mierzyć?
Wskaźniki produkcyjne (KPI – Key Performance Indicators) pełnią kluczową rolę w zarządzaniu zakładem przemysłowym, niezależnie od jego wielkości czy rodzaju produkcji. Dzięki nim możliwe jest identyfikowanie słabych punktów, planowanie działań usprawniających oraz obiektywna ocena postępów. Oto najważniejsze wskaźniki na produkcji, które warto systematycznie monitorować:
- Wydajność produkcji – oznacza ilość wytworzonych jednostek produktu w określonym czasie (np. sztuk/godzinę). To podstawowy wskaźnik efektywności operacyjnej. Wydajność wskazuje, czy procesy produkcyjne przebiegają płynnie, czy też pojawiają się opóźnienia, które ograniczają tempo realizacji zleceń.
- Współczynnik jakości – określa udział wyrobów spełniających wymagania jakościowe względem ogólnej liczby wyprodukowanych sztuk. Niska wartość tego wskaźnika może świadczyć o problemach w procesie technologicznym, nieodpowiednim szkoleniu pracowników lub błędach w zaopatrzeniu materiałowym.
- Czas cyklu – to czas potrzebny na wyprodukowanie jednej jednostki produktu od momentu rozpoczęcia do zakończenia danego etapu produkcji. Im krótszy i bardziej stabilny czas cyklu, tym wyższa efektywność i lepsze wykorzystanie zasobów.
- Poziom przestojów – mierzy czas, w którym maszyny lub linie produkcyjne pozostają nieaktywne w stosunku do planowanego czasu pracy. Przestoje mogą być planowane (np. konserwacja) lub nieplanowane (awarie, brak materiału) – oba typy powinny być analizowane osobno. Wysoki poziom przestojów oznacza straty i nieefektywność.
- Wskaźnik wykorzystania maszyn – pokazuje, jak intensywnie wykorzystywane są zasoby techniczne w porównaniu do ich pełnych możliwości. Pomaga określić, czy park maszynowy jest optymalnie zarządzany, czy też może wymaga rozbudowy lub reorganizacji.
- Scrap rate (poziom odpadu) – wskazuje procent wyrobów, które nie nadają się do sprzedaży lub wymagają poprawek (reworku). Jest to jeden z kluczowych wskaźników związanych z jakością i kosztem produkcji – im niższy scrap rate, tym większa efektywność i oszczędności materiałowe.
- Koszt jednostkowy produkcji – to całkowity koszt przypadający na jedną jednostkę produktu. Uwzględnia zarówno koszty materiałowe, robocizny, jak i koszty pośrednie (np. energia, amortyzacja). Pomaga kontrolować rentowność produkcji i podejmować decyzje cenowe oraz inwestycyjne.
- OEE (Overall Equipment Effectiveness) – to złożony wskaźnik, który łączy trzy kluczowe aspekty: dostępność (czas pracy maszyny), wydajność (szybkość produkcji) oraz jakość (odsetek wyrobów zgodnych). OEE daje najbardziej kompleksowy obraz efektywności technicznej i organizacyjnej produkcji.
Wśród wymienionych wskaźników to właśnie OEE wyróżnia się jako najważniejszy i najbardziej uniwersalny. Dlaczego? Ponieważ integruje w jednej liczbie wszystkie główne czynniki wpływające na efektywność produkcji. W ten sposób pozwala zidentyfikować nie tylko to, że produkcja działa poniżej oczekiwań, ale również – w której dokładnie sferze pojawia się problem: czy chodzi o awarie i przestoje, o zbyt wolną pracę maszyn, czy też o dużą ilość braków. Właśnie ta wszechstronność sprawia, że OEE bywa określany mianem „króla wskaźników produkcyjnych”.
Jednak warto pamiętać, że żaden wskaźnik nie funkcjonuje w próżni. Ich wartość ujawnia się dopiero w kontekście – gdy są powiązane z celami biznesowymi, analizowane regularnie i służą jako baza do podejmowania działań optymalizacyjnych. W praktyce najbardziej skuteczne firmy to te, które łączą OEE z pozostałymi miernikami, tworząc spójny system zarządzania produkcją oparty na danych.
OEE – król wskaźników efektywności produkcji
OEE to wskaźnik całkowitej efektywności maszyn, który pozwala określić, w jakim stopniu możliwości techniczne maszyn są wykorzystywane w praktyce. Wskaźnik ten:
- identyfikuje straty produkcyjne,
- umożliwia szybką ocenę sytuacji,
- pozwala porównywać efektywność różnych maszyn czy linii produkcyjnych.
Na OEE składają się:
- Dostępność – rzeczywisty czas pracy w stosunku do zaplanowanego,
- Wydajność – faktyczna prędkość pracy maszyny wobec jej maksymalnych możliwości,
- Jakość – procent produkcji zgodnej z wymaganiami.
Jak poprawnie liczyć OEE?
OEE = Dostępność x Wydajność x Jakość
Przykład:
- Planowany czas pracy: 8 godzin,
- Czas pracy rzeczywisty: 7 godzin,
- Dostępność = 7/8 = 87,5%
- Teoretyczna liczba sztuk: 1000,
- Wyprodukowane sztuki: 900,
- Wydajność = 900/1000 = 90%
- Zgodne produkty: 855,
- Jakość = 855/900 = 95%
OEE = 0,875 x 0,9 x 0,95 = 74,8%
Czego nie mówi Ci sam wskaźnik OEE?
Choć OEE dostarcza ogólnego obrazu, nie pokazuje:
- konkretnych przyczyn przestojów – OEE jedynie pokazuje, że przestoje miały miejsce i w jakim stopniu wpłynęły na dostępność, ale nie wskazuje, czy były one wynikiem awarii technicznych, braku operatora, braku materiału, planowanej konserwacji czy np. błędów logistycznych. Bez osobnej analizy przyczyn źródłowych (np. za pomocą narzędzi takich jak analiza Pareto, RCA, metoda 5x Why), nie wiadomo, gdzie należy podjąć konkretne działania naprawcze.
- rodzaju defektów jakościowych – wskaźnik jakości w OEE ujmuje tylko ogólny procent wyrobów zgodnych z wymaganiami, ale nie rozróżnia, czy błędy wynikały z problemów z maszyną, niewłaściwego ustawienia parametrów, wad materiału czy błędów ludzkich. Nie pokazuje też, które produkty lub partie były wadliwe. To ograniczenie może utrudniać właściwą reakcję oraz optymalizację procesu.
- zmienności między zmianami – OEE jako wskaźnik zagregowany często nie uwzględnia różnic między konkretnymi zmianami roboczymi, operatorami, typami maszyn czy nawet produktami. Może się zdarzyć, że ogólny wynik jest zadowalający, ale jedna ze zmian systematycznie wypada gorzej – a tego OEE nie ujawni bez podziału danych. Analiza per zmiana lub per linia jest konieczna, jeśli chcemy zidentyfikować źródła różnic wydajności i wprowadzać celowane działania doskonalące.
- poziomu zaangażowania pracowników – OEE nie jest w stanie uchwycić „miękkich” aspektów produkcji, takich jak motywacja, morale zespołu, komunikacja czy kultura pracy. Tymczasem czynniki te często mają bezpośredni wpływ na efektywność – np. brak zaangażowania może skutkować większą ilością błędów, spowolnieniami i słabszą reakcją na zakłócenia.
Z tych powodów OEE powinno być traktowane nie jako cel sam w sobie, ale jako punkt wyjścia do dalszej analizy i doskonalenia procesu. W praktyce najbardziej wartościowe informacje uzyskuje się dopiero wtedy, gdy OEE zestawia się z:
- danymi o przyczynach przestojów (np. rejestrowanymi przez operatorów lub automatycznie przez system MES),
- rejestrami błędów jakościowych,
- raportami dziennymi z produkcji, informacjami o warunkach pracy i organizacji zmian,
- danymi z planowania produkcji i logistyki.
Dopiero wtedy wskaźnik OEE nabiera pełnego znaczenia jako narzędzie operacyjne i strategiczne. Sam w sobie jest jedynie liczbą – to interpretacja i działanie na podstawie jego komponentów czynią go prawdziwie użytecznym.
OEE w praktyce – jak go wdrożyć i wykorzystać?
- Zacznij od edukacji zespołu – wytłumacz, czym jest OEE i jak się je liczy.
- Zbieraj dane – ręcznie lub automatycznie z maszyn.
- Wybierz metody prezentacji wyników (np. dashboardy, raporty dzienne).
- Analizuj i reaguj – szukaj źródeł strat i wąskich gardeł.
- Wyznacz cele i KPI cząstkowe dla poszczególnych działów.
- Kontroluj zmiany i poprawiaj – wdrażaj filozofię ciągłego doskonalenia.
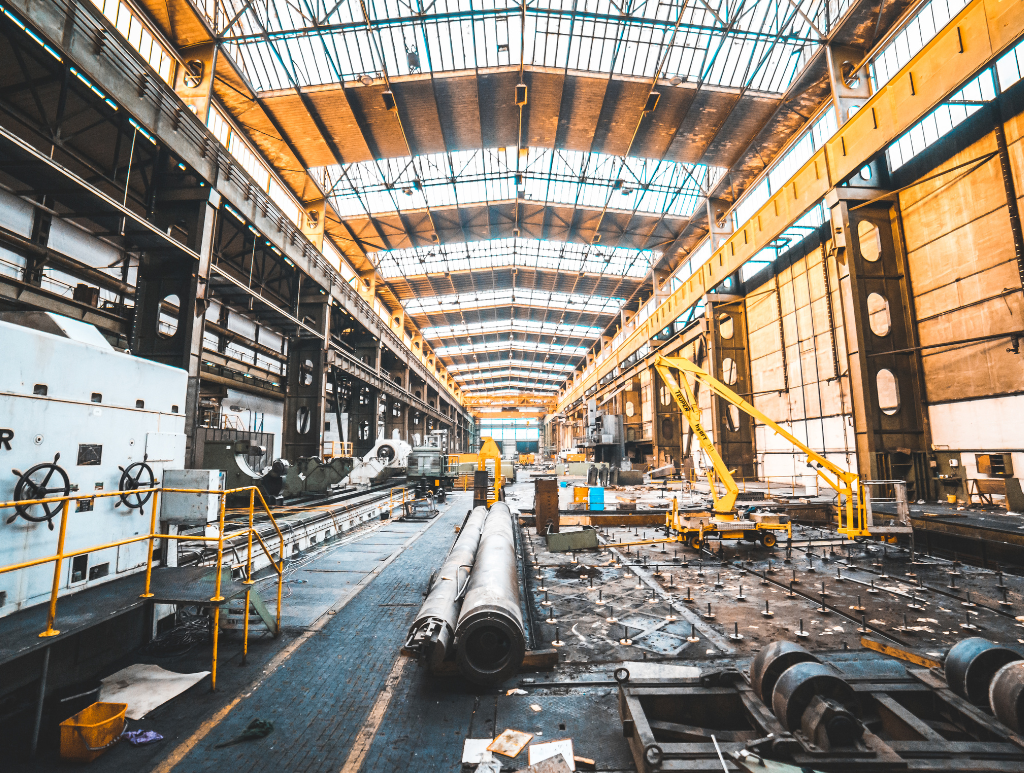
Rozwijanie produkcji dzięki wskaźnikom
Błędy przy interpretacji wskaźników produkcyjnych
- Brak kontekstu – Sama wartość wskaźnika niewiele mówi, jeśli nie znamy szczegółów dotyczących specyfiki danego procesu produkcyjnego, rodzaju maszyn, czy charakterystyki wyrobów. Bez tego trudno wyciągnąć trafne wnioski i podjąć skuteczne działania naprawcze.
- Zbyt duże uproszczenia – Prowadzi do ignorowania kluczowych czynników wpływających na wyniki, takich jak plany produkcyjne. Przykładowo, brak uwzględnienia częstych zmian asortymentu, krótkich serii czy niestabilnych harmonogramów może powodować błędne przypisanie przyczyn niskiej efektywności wyłącznie maszynom lub operatorom, zamiast uwzględnić ograniczenia planistyczne.
- Brak rozbicia na zmiany lub maszyny – Analiza tylko zagregowanych danych może ukrywać nierówności i słabsze ogniwa, które wymagają indywidualnego podejścia. Bez takiego podziału trudno zidentyfikować, które obszary faktycznie potrzebują poprawy i jakie działania przyniosą największy efekt.
- Nieadekwatne cele KPI – Np. sztucznie zawyżone wymagania. Takie nierealistyczne wymagania mogą demotywować pracowników i prowadzić do manipulacji danymi lub działań nastawionych jedynie na poprawę wskaźników, a nie rzeczywistą efektywność procesu.
Alternatywy i uzupełnienia dla OEE
Choć OEE jest bardzo uniwersalne, warto je uzupełnić innymi wskaźnikami, np.:
- MTBF (Mean Time Between Failures),
- MTTR (Mean Time To Repair),
- TEEP (Total Effective Equipment Performance),
- Efektywność energetyczna,
- Produktywność operatorów.
Jak dobrać wskaźnik do typu produkcji?
Dobór odpowiednich wskaźników produkcyjnych musi być ściśle dopasowany do charakteru produkcji, ponieważ różne typy procesów mają odmienne wyzwania i cele.
Produkcja jednostkowa
W przypadku produkcji jednostkowej, gdzie wytwarzane są pojedyncze, często unikatowe produkty, kluczowe są wskaźniki takie jak czas cyklu, koszt jednostkowy oraz jakość. Tu najważniejsze jest kontrolowanie efektywności realizacji pojedynczych zamówień, minimalizacja kosztów na jeden produkt oraz zapewnienie wysokiego poziomu jakości, ponieważ każdy wyrób jest istotny i często niepowtarzalny.
Produkcja seryjna
Dla produkcji seryjnej, gdzie wytwarzane są partie produktów o większej powtarzalności, istotne stają się wskaźniki takie jak OEE, takt time czy wskaźnik przestojów. OEE pozwala monitorować efektywność wykorzystania maszyn i procesów w całym cyklu produkcyjnym, takt time pomaga dostosować tempo produkcji do zapotrzebowania, a analiza przestojów umożliwia identyfikację i eliminację przyczyn zatrzymań, co jest kluczowe przy powtarzalnej produkcji.
Produkcja masowa
W produkcji masowej, charakteryzującej się dużymi wolumenami i ciągłym wytwarzaniem tych samych produktów, znaczącą rolę odgrywają wskaźniki takie jak OEE, scrap rate (wskaźnik odpadów) oraz czas przezbrojeń. Tu ważne jest maksymalne wykorzystanie parku maszynowego, minimalizacja strat materiałowych oraz skracanie czasu przezbrojeń, które wpływają bezpośrednio na ciągłość i wydajność produkcji.
Wskaźniki a rozwój firmy – kiedy prostota, kiedy zaawansowanie?
Na początkowym etapie rozwoju firmy warto skupić się na prostych, łatwych do zrozumienia i szybkich do zmierzenia wskaźnikach, takich jak wydajność, jakość czy czas przestojów. Takie podstawowe miary pozwalają zbudować fundamenty zarządzania produkcją, szybko zidentyfikować główne problemy oraz wypracować pierwsze standardy działania. Proste wskaźniki sprzyjają zaangażowaniu pracowników i ułatwiają komunikację na wszystkich poziomach organizacji. W miarę jak firma rośnie i procesy produkcyjne stają się bardziej złożone, konieczne staje się wprowadzanie bardziej zaawansowanych narzędzi i metod pomiaru:
- wprowadzanie automatyzacji pomiaru (MES),
- łączenie wskaźników z analizą kosztów,
- tworzenie pulpitów menedżerskich,
- analizowanie trendów i korelacji między wskaźnikami.
Jakie narzędzia wspierają monitorowanie wskaźników?
- Excel, Google Sheets – dobry początek.
- MES i SCADA – systemy do monitorowania maszyn w czasie rzeczywistym.
- ERP z modułem produkcji – np. ZaPro, Prodio.
- BI (Business Intelligence) – Power BI, Tableau – do analizy danych.
Najważniejszy wskaźnik to… ten, który prowadzi do działania
Nie ma jednego uniwersalnego KPI dla każdej firmy. OEE wyróżnia się jako wskaźnik bardzo uniwersalny, ale najważniejsze jest, aby dane prowadziły do:
- podejmowania konkretnych działań,
- eliminacji strat,
- zaangażowania zespołu w poprawę wyników.
Bo prawdziwym celem wskaźników nie jest samo ich mierzenie, ale zmiana na lepsze.
W świecie produkcji wskaźniki KPI to podstawa skutecznego zarządzania. Spośród nich OEE pozostaje najbardziej kompleksowym i uniwersalnym narzędziem pomiaru efektywności. Klucz tkwi jednak nie w samych liczbach, ale w ich interpretacji i wykorzystaniu do realnych zmian na hali produkcyjnej. Dlatego właśnie OEE, choć nie doskonałe, jest najważniejszym wskaźnikiem na produkcji – bo pokazuje, gdzie działać, by osiągać więcej.